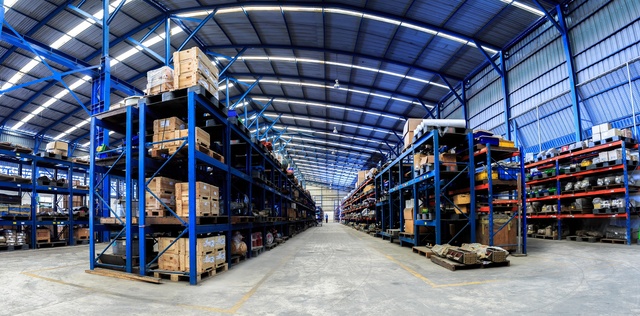
Many people aren’t very familiarized with warehousing, and just how their products get from point A (the click of the “purchase” button”) to point B (their house). A major part of the success of companies, large, medium, or small, is the strength of their warehousing. In this post, we’ll give you a behind-the-scenes overview of how warehousing works. Here are some of the (many) things that go on in a warehouse from the moment you order your product.
Storage
Warehouses, especially for large companies, tend to be massive. For example, the Amazon fulfillment center in Baltimore covers 23 acres—one million square feet. Warehouses are usually divided into four sections: inbound area (products that are arriving), storage area (products that have arrived), outbound area (products leaving), and yard (products going onto transport). Cross-docking may be necessary, and the size of each of these sections depends on the company itself.
Warehouses have different levels of inventory on hand, generally lasting anywhere from half-a-month to ninety days, depending on the location and the warehouse itself. When new products arrive at the warehouse, the goods received are matched with the original purchase order during the staging of goods. Quality control is key—quality control is a visual inspection of the products, checking to make sure that there is no damage or aesthetic inaccuracies that need to be addressed. If everything checks out, the products go through a system-directed storage process that organizes the goods based on several factors.
Products can be organized into “ABC categories.” Examples of the dimensions to be considered when sorting include: item carrying cost, sales amount, sales quantity, inventory value, and more. Your “A” category should consist of your top 20% products, your “B” should consist of top 30%, and “C” should consist of the remaining 50%. Warehouses should count their inventories using cycle-counting, which is where a subset of inventory in a specific area is counted on a specific day in order to make sure that there are no numeric discrepancies between what is on-hand and what is in the computer.
Picking
Order picking is the next major stage in the warehouse process. There are several different types of picking; piece-picking, case-picking, and pallet picking. Each of these have a variety of different subcategories, but the overall goals of each are the same: efficiency and high productivity. The goal is also a short cycle time, which is the amount of time an order takes to get from the entry stage to the shipping dock.
-
Piece-picking operations, such as repair parts distributors and mail order catalogs, involve systems where individual items (as opposed to packages of items) are picked.
-
Case-picking uses items such as a pallet pick, carousel, and other equipment to choose a bulk unit of a product.
-
Pallet-picking is also known as unit-load picking. Orders are picked, and the picker uses a lift to move the entire pallet to the shipping area to a staging lane for unloading.
Retrieval
Retrieval is the last stage of the warehouse process. Retrieval involves getting the item and loading it for shipping. ASRS systems often come into play at this part. ASRS are automated storage and retrieval systems. These are computer-controlled systems that help warehouses function by using horizontal carousels or vertical lift modules to help a warehouse maximize space and speed. Carousel models involve bins that rotate on a horizontal track, and they are one of the top-performing systems for warehouse storage. Vertical lift models operate most optimally in warehouses with a lot of overhead storage space. They store things in vertical configurations.
There is so much that goes on within a warehouse from the moment an order is entered to when it is transported to the shipping location. As robotics and computer science continues to advance, warehouses will grow faster, more efficient, and streamlined.