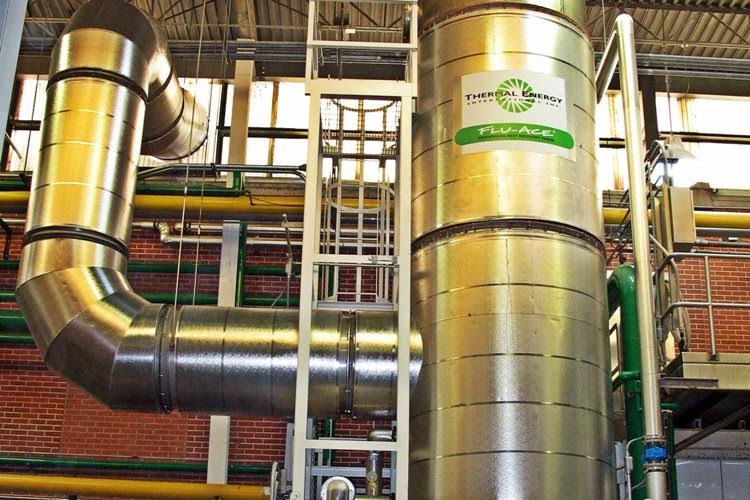
Reducing harmful emissions and using resources more efficiently is not only good for the environment, it is also good for business competitiveness and profitability. A key resource for most industrial companies is energy. Using less energy equals lower costs and less greenhouse gas emissions. Conversely, wasted energy equals wasted money and unnecessary greenhouse gas emissions.
With between 20 to 50% of all industrial energy input being lost as waste heat in the form of hot exhaust gases, cooling water, and heat lost from hot equipment surfaces and heated products, large cost saving opportunities and increased productivity can be achieved by companies who can use energy more efficiently – even with the prevailing lower energy prices we have been seeing in recent times. And, while many industrial companies are taking some positive action, substantial energy efficiency opportunities for manufacturers still remain. Put simply, energy is not being used as efficiently as it could be. This efficiency gap is found across all sectors, from food and beverage, pulp and paper, and healthcare, to pharmaceuticals, chemical, petrochemical, etc.
There are numerous, largely still untapped, cost–effective technologies that are not being employed. We’re not talking about experimental technologies or large research and development projects, but existing, proven and commercially available technologies that could substantially improve the energy end-use.
Canadian company, Thermal Energy International, has two such proven technologies that help industrial companies use energy more efficiently – reducing the total amount of energy consumed by industrial processes and reducing harmful greenhouse gas emissions at the same time. While their customers include Fortune 500 and other leading multinational companies across many industries, the company does not disclose the names of its customers for competitive reasons. Let’s take a look at how Thermal Energy’s two, existing and commercially available technologies help industrial operations improve their energy efficiency and profitability.
Typically about 18% of the energy used in a boiler plant is lost up the boiler stack. Thermal Energy’s proprietary FLU-ACE direct contact condensing heat recovery systems effectively recover this waste energy and uses it to preheat a heat sink – this could be water for your space heating, domestic hot water, boiler feed water, or outside air heating.
Up to 20% of a facility’s steam is lost through steam trap systems. About 10% of conventional mechanical traps fail each year due to wear of mechanical parts. Mechanical traps tend to have large orifice sizes, so when failing open, or even partially open, the steam losses can be substantial. Thermal Energy’s venturi-orificed GEM steam traps on the other hand have much smaller orifices. In addition, they have no moving parts that can wear, seize and fail, so they require less maintenance than mechanical steam traps. Less steam lost equals more efficient. Less maintenance and replacement equals less downtime, higher productivity and increased profitability.
According to Thermal Energy’s website, these two energy efficiency products can recover from 20% to 30% of the energy wasted by many industrial and institutional operations, and reduce GHG emissions by comparable amounts. Project paybacks are typically between one and five years.
The energy savings and emissions reductions that can be achieved with Thermal Energy’s and other existing technologies is quite substantial. The high return on investment makes industrial energy efficiency the low hanging fruit for helping meet our society’s increasing demand for energy while reducing harmful emissions.
Energy efficiency is among the cheapest and cleanest energy resources available. In fact, according to a recent report from the American Council for an Energy Efficient Economy, “How Much Does Energy Efficiency Cost,” the “new” power resulting from energy efficiency efforts is substantially less expensive than the cost of power that would be generated by new power plants (including wind farms and utility scale solar power). Yet for industry, and manufacturing operations in particular, the quickest and most effective source of lower energy bills remains largely under exploited.
The technologies are here today. Proven results have been achieved. The facts are published. There is no reason why high energy users such as manufacturers shouldn’t strive to achieve maximum energy efficiency and with it, profitability.